O que significa “ser Lean”?
“Convido a todos a fazer uma reflexão sobre o que é “ser Lean” (Lean Thinking – Pensamento Enxuto). Antigamente, quando me perguntavam o que é Lean, minha resposta era sempre a definição técnica. Porém, fazendo uma reflexão sobre o tema, chego a conclusão de que ainda falta, por grande parte das pessoas, um maior entendimento dessa Filosofia.
Não adianta apenas copiar e adaptar as técnicas ensinadas pela Toyota, precisamos pensar Lean e ser enxutos em qualquer atividade que façamos. Isso significa que devemos buscar fazer toda tarefa da melhor maneira (qualidade) e no menor tempo possível (produtividade). Para realmente termos esse pensamento enxuto, é necessário muito mais do que conhecer as técnicas do Lean.
Na execução de qualquer trabalho, a busca pela redução dos desperdícios é o que irá aumentar a produtividade. Porém, isso não pode comprometer a qualidade da entrega. É necessário encontrar o ritmo ideal de trabalho das equipes, proporcionando equilíbrio entre qualidade e produtividade. Não devemos acelerar as pessoas além do seu ritmo ideal, pois isso pode gerar falhas no processo produtivo ou na entrega de um serviço. Além disso, a procura constante pela melhoria na qualidade do trabalho, evidencia a todos a importância de estar sempre estudando e aprendendo novas maneiras de trabalhar.
Lembre-se: não adianta aplicar as ferramentas do Lean se o mindset da equipe ainda não estiver voltado para os princípios básicos da supressão de desperdícios e melhoria contínua. Também não adianta apenas cobrar dos outros essa forma de pensar se não a praticarmos em todas esferas. Saber utilizar os recursos de maneira inteligente é um jeito de ser Lean, e pode ajudar a sua empresa, o país e até o mundo a caminhar no sentido da inovação e da sustentabilidade.
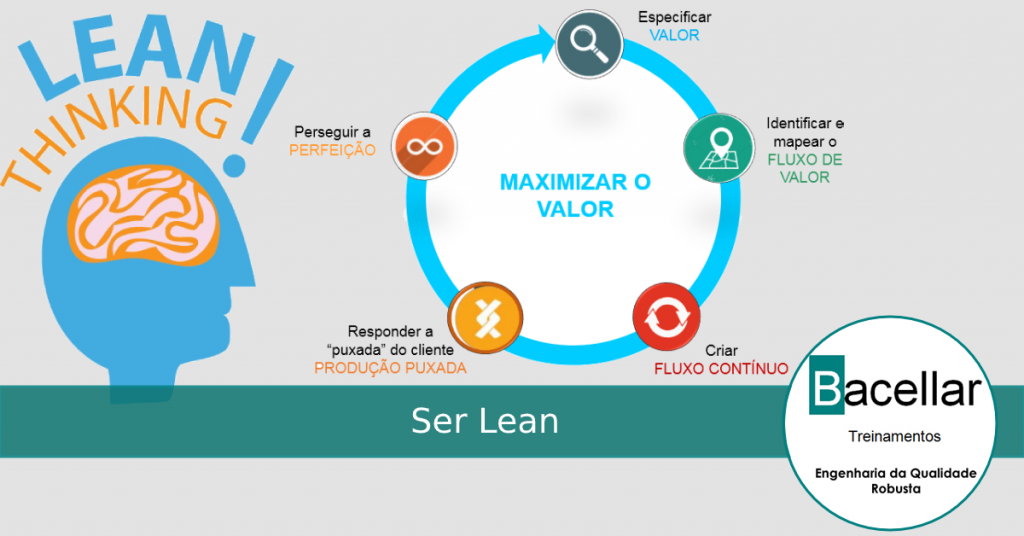
Enquanto nós, gestores, funcionários ou qualquer agente de mudança, não fizermos a revolução interna no nosso dia a dia, teremos dificuldade em revolucionar as organizações. Se queremos “ser Lean”, temos que pensar desde o momento em que acordamos de maneira enxuta, planejando nossa rotina e estando atento para os desperdícios e obstáculos que podemos nos deparar. Cada dia nos perguntar o que não saiu como planejado e pensar como melhorar para o dia seguinte. Essa ideia serve para tarefas simples do dia a dia, mas também para a resolução dos problemas mais complexos no ambiente corporativo. Isso é ser Lean.”
Luiz Ribeiro Bacellar